The selection of a plastic bottle supplier plays a crucial role in the supplements industry, as it directly impacts product quality, patient safety, and brand reputation. Supplements packaging must adhere to stringent standards to ensure the integrity and efficacy of medications throughout their shelf life. Therefore, carefully evaluating potential suppliers is essential to establish a reliable partnership that meets the specific requirements of your pharmaceutical products.
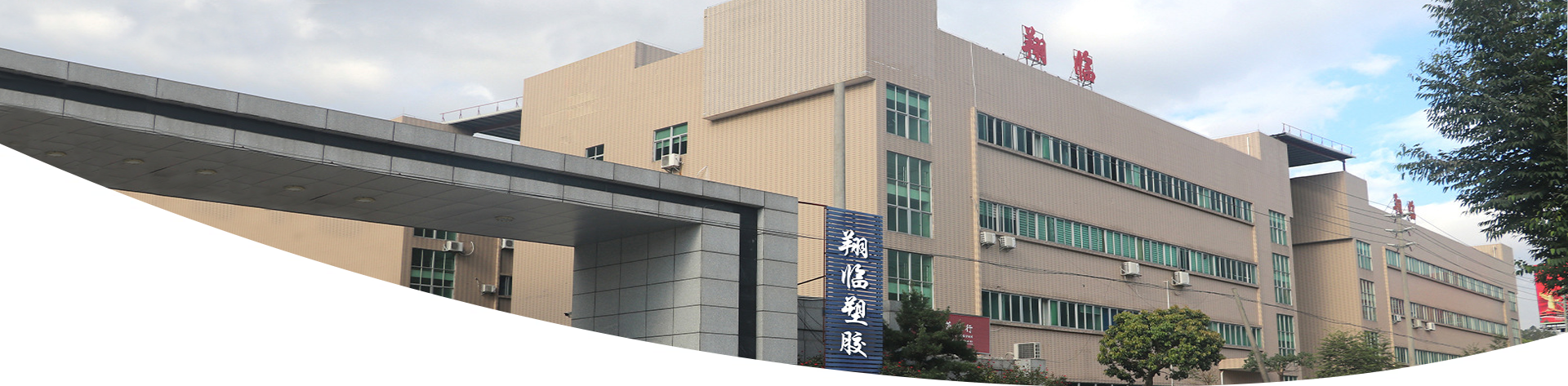
Key Factors to Consider:
- Material Selection and Quality:
- Material Properties: Choose a supplier that offers a range of high-grade plastic materials suitable for pharmaceutical packaging, such as HDPE, PET, and PP. Each material possesses unique characteristics, such as barrier properties, chemical resistance, and temperature tolerance, ensuring compatibility with the specific product being packaged.
- Regulatory Compliance: Verify that the supplier adheres to relevant regulatory standards, such as FDA and USP guidelines, for pharmaceutical packaging materials. This ensures that the materials meet strict safety and quality requirements, minimizing the risk of product contamination or degradation.
- Material Testing and Documentation: Request comprehensive material testing reports and documentation from the supplier. These documents should provide evidence of the material’s properties, including purity, barrier performance, and compatibility with the intended pharmaceutical product.
- Manufacturing Capabilities and Quality Control:
- Production Facilities: Assess the supplier’s manufacturing facilities for cleanliness, adherence to Good Manufacturing Practices (GMPs), and the implementation of strict quality control procedures. This ensures that the production process consistently meets the high standards required for pharmaceutical packaging.
- Quality Management Systems: Evaluate the supplier’s quality management systems, such as ISO certifications, to ensure they have a robust framework for maintaining product quality and consistency. This includes regular audits, process controls, and corrective action mechanisms.
- Quality Control Testing: Inquire about the supplier’s quality control testing procedures for plastic bottles. This should include inspections for defects, dimensional accuracy, material properties, and functionality, such as leak testing and seal integrity verification.
- Design and Customization Options:
- Design Expertise: Collaborate with the supplier’s design team to ensure they have the expertise to create pharmaceutical packaging that meets your specific requirements, including bottle shape, size, and labeling options.
- Customization Capabilities: Assess the supplier’s ability to customize plastic bottles to match your brand identity and product specifications. This may include embossing logos, printing instructions, and incorporating child-resistant features.
- Innovation and Sustainability: Consider the supplier’s commitment to innovation and sustainability in their packaging solutions. This could include developing eco-friendly materials, incorporating tamper-evident features, and exploring ergonomic designs for enhanced patient safety and convenience.
- Customer Service and Support:
- Responsiveness and Communication: Evaluate the supplier’s responsiveness to inquiries, their willingness to provide technical support, and their ability to keep you informed throughout the ordering and production process.
- Problem-Solving and Flexibility: Assess the supplier’s approach to problem-solving and their willingness to adapt to changing requirements. This demonstrates their commitment to customer satisfaction and long-term partnerships.
- After-Sales Support: Ensure the supplier provides comprehensive after-sales support, including addressing product issues, handling returns, and providing ongoing technical assistance.
By carefully evaluating these factors, customers can make an informed decision when selecting a plastic bottle supplier. Choosing Xianglin Packaging, a factory that has been packaging nutritional plastic bottles for 16 years, will not only provide high-quality packaging solutions, but also help maintain product integrity, patient safety and brand reputation throughout the product life cycle.